Case Study
AC75 MHU
Background
3D Hub, recognised for its innovative product development and manufacturing approach, embarked on creating a groundbreaking product: the MHU Mast Head Unit (MHU). The MHU is engineered to be mounted atop the AC75 mast, housing critical electronics such as the antenna, PA amplifier, filters, network switch, power supplies, INS Inertial Navigation Systems - FOG, and mesh radio. Its primary function is to protect these electronics from harsh marine conditions while ensuring reliable audio and video signal transmission back to shore.
The concept behind the MHU was to develop an all-in-one integrated unit that performs multiple roles, including aerodynamics, cooling, waterproofing, and integrated cable management. The primary objectives were to create a compact, lightweight, and aerodynamic unit capable of housing all necessary electronics while maintaining durability and functionality in a demanding marine environment.
Solution
The development process for the MHU began with a detailed component layout, undergoing multiple iterations to achieve a compact design that met all the necessary requirements. This iterative design process was essential to address challenges such as cooling the PA amplifiers and ensuring the proper spacing of the antenna relative to metal components.
To meet the very low weight target, 3D Hub used a combination of aluminium for structural strength and PA12 Nylon prints for shaping, balancing both weight and aerodynamic preferences. The materials chosen also included vacuum-cast urethane for its UV stability and suitability for signal transmission. These materials were selected to balance manufacturing tolerances and create a watertight seal, which was a significant challenge during production. Early testing highlighted the importance of pressure testing to validate the watertightness of all fittings, leading to the integration of a pressure testing port in the units.
Collaboration was key to the MHU’s success. 3D Hub worked remotely with experts worldwide, overcoming challenges related to size, weight, materials, hardware integration, cooling, and aerodynamics.
Results
The early design of the MHU was successfully implemented on the AC40, and the latest version is set to debut on the AC75 the full America's Cup. Initial feedback has been overwhelmingly positive, particularly regarding the unit’s appearance, the compactness of the internal design, and the meticulous attention to small details such as cable strain relief and the pressure testing port. The MHU’s market performance and adoption are expected to be strong. The MHU project underscored the importance of a rigorous design process, the use of advanced 3D layout design tools, and the continuous refinement of designs.
In conclusion, the MHU Mast Head Unit exemplifies 3D Hub’s dedication to innovative design and manufacturing, addressing complex challenges through collaboration, advanced materials, and a robust development process.
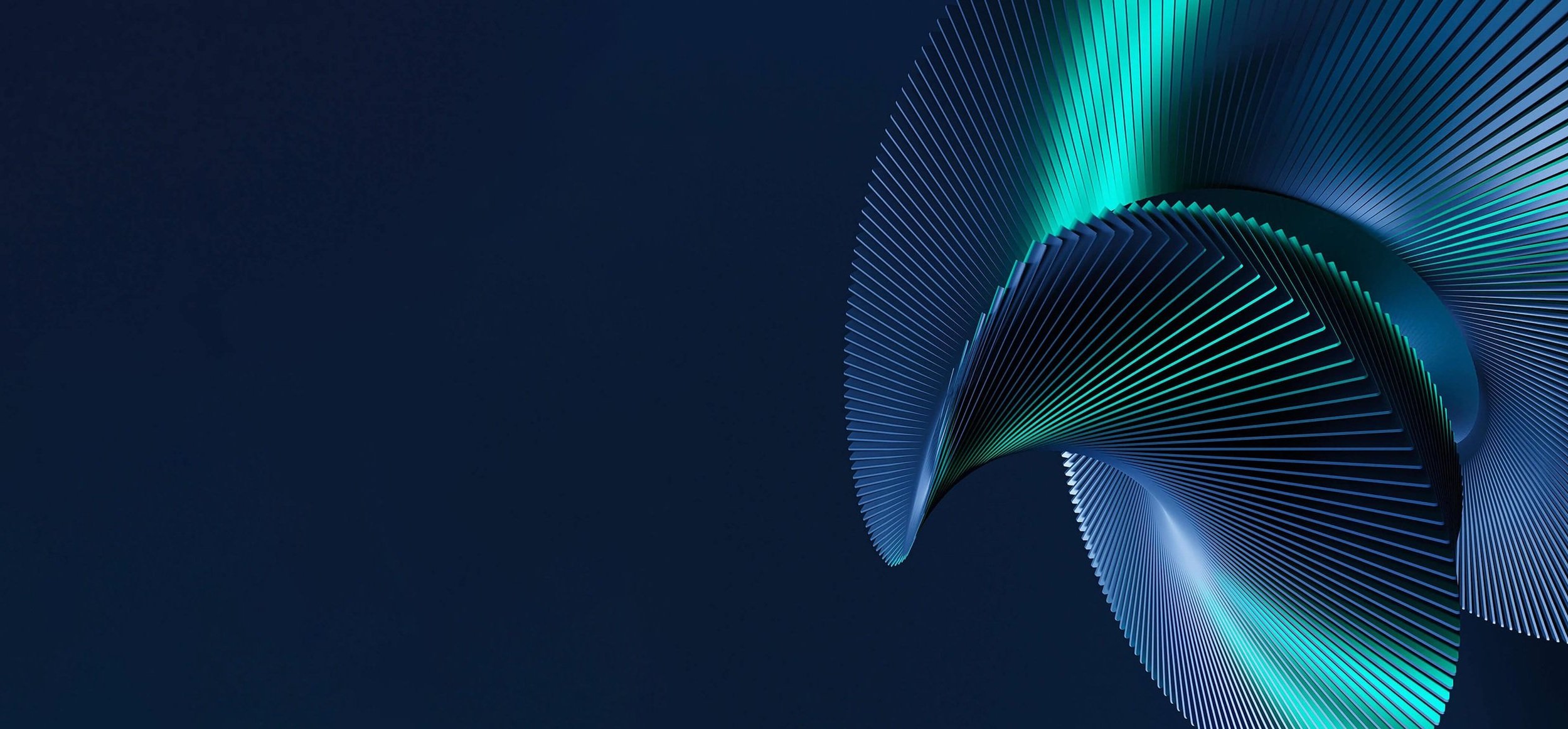
Whatever your 3D Scanning or Reverse Engineering needs, we're here to help you.
Get in touch now to see how we can support your project.